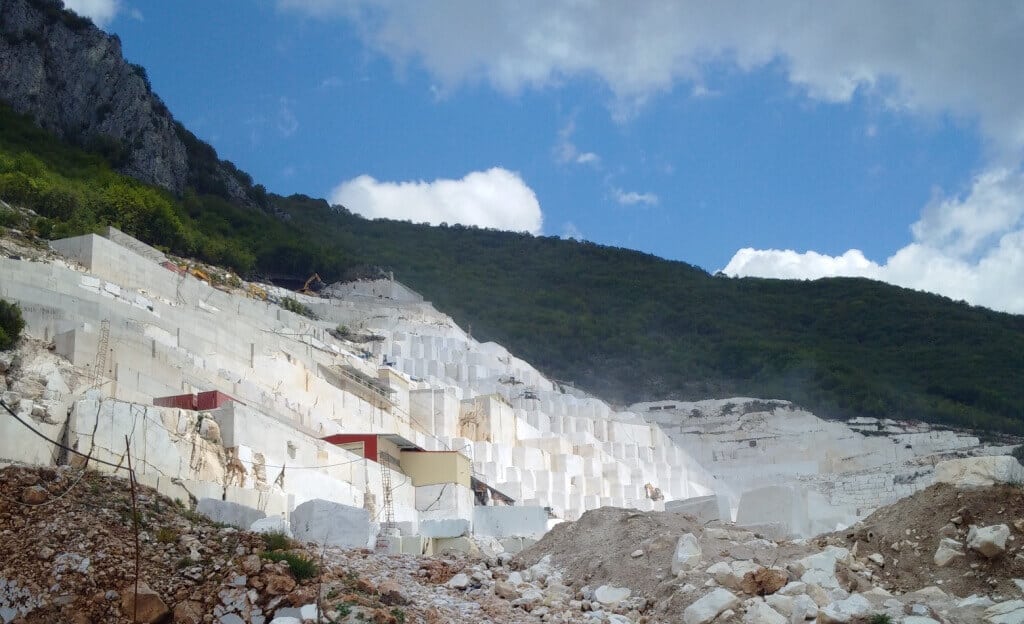
Quarry and Manufacturing Quality Control of Marble
In this post we are going to describe the “Quality Control Process in Quarry and Factory of Natural Stone“; the first phase at origin of any Stone Project.
Marble and any kind of Stone are characterized by their condition of “Natural”. This feature makes each piece into a unique and singular element. However that singularity requires an exhaustive Quarry Quality Control but also during its manufacturing, delivery and installation.
Since 2003, CE marking has been compulsory for natural stone manufacturers, to sell their products in the UE . This certificate guarantees compliance with a series of procedures and requirements that vary according to the type of product, and works as a guarantee of harmonisation between products from the EU. However, this rule is only applicable to products coming from the EU.
Although the CE mark is a guarantee of quality, it does not exempt each element from its essential characteristic, “Uniqueness”. Therefore, it is advisable to carry out a Quarry and Manufacturing Quality Control of the Stone to ensure a harmonic arrangement of every tiles prior to installation.
It is importan to emphasize that the more exhaustive the quality control, the greater the level of trust between the parties (supplier-customer).
Precisely the differentiation between some suppliers and others, is given by the capacity of these, to assure the quality of the supplied materials, based not only on the physical-mechanical characteristics of the material, but that this one fulfills the requirements of homogeneity/uniformity previously agreed. Only then, a harmonic result of our project can be guaranteed.
¿What is Quarry and Manufacturing Quality Control of Stone?
In most cases, this Quality Control is carried out by the supplier itself. Nevertheless and for obvious reasons, it is precisely in this process that the figure of the Natural Stone Consultant takes on special importance, given its impartiality as an external and independent professional.
The objective of this post is to show a guide on how to carry out a procedure for Quality Control at Origin, that is, one that covers the phases of quarrying and manufacturing.
We have divided this procedure in 3 stages:
1. Quarry Quality Control of Stone
1. a. Location of the specified sample in the quarry
It is a priority to locate the area from which the blocks will be extracted in the the quarry, to be sent afterwards to the factory for production, following the specifications of the project.
1. b. Location of the operational fronts of the quarry
Visual inspection of the operational fronts of the quarry, to verify the front from which the material will be extracted is the appropriate one, according to the requirements of the project.
It is necessary to understand the lateral variations of the operational fronts of the quarry, in terms of tonality, veining, cracks, etc.
Depending on the size of the project, and the different areas and phases to install the stone at site, it can be organized and prioritized with the quarry owner even the direction of extraction of the blocks.
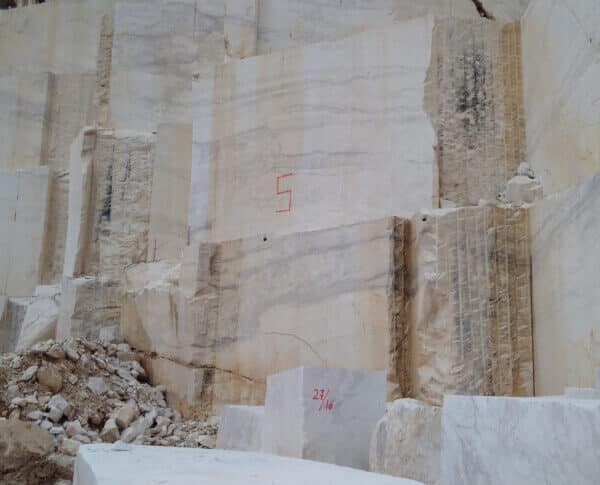
1. c. Marking and labelling of the blocks in the quarry
It consists of identifying the blocks with the different fronts of the quarry, to ensure that they are from the same source and according to the established extraction plan.
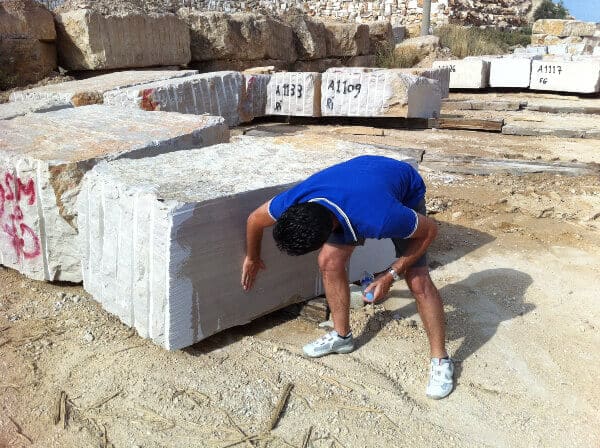
2. Inspection during manufacturing
2. a. Monitoring of the blocks from the quarry
At this stage, the reception of the blocks is monitored according to the selected fronts. Hereinafter they are introduced in the factory according to the priorities of the project.
2. a. Random slabs inspection
A visual inspection of the production of slabs is carried out in the cutting process, as well as in the resin and polishing processes.
A random inspection of the slabs is performed once they are finished. It is compulsory to asure the same labelling for the slabs as the original blocks, only so the correct tracking can be made throughout the process.
Image 5. Random slabs inspection.
2. b. Identification of the marble slabs and tiles in factory
Identification of the tiles with the original Slabs and the area of installation according to the shopdrawings.
Image 6. Slabs and tiles inspection in factory. Crumar Project, Spain
2. d. Inspection of tiles during production
Inspection from the production line to the packing, checking tonalities, sizes and thickness, and lateral angles following the standards. This inspection must be done before packing.
Image 7. Tiles inspection during manufacturing
2. e. Labelling of crates
The wooden crates are marked in the sides with different colors and area according to the place of installation.
New inspection of material to the 15% of the crates. About 4 o 6 pieces of each crate are laid on the floor to be checked: number of tiles per crate, tonality and sizes.
Image 8. Crates labelling in factory.
If at the last inspection the material is in accordance with the project requirements, the crates will be spray-marked and labelled.
The Marble is now ready for shipment.
3. Quality control before delivering
Supervision of container loading, verifying that the crates are correctly identified and the wood has been fumigated and sealed.
Once the marble is inside the container, it is registered and sealed and a Certificate of Compliance is issued.
Image 9. Inspection prior to transport
From then on, new stages of the project are opened in which an exhaustive quality control must be carried out, particularly in the installation process. You will find more information about Quality Control during Stone installation in future posts.
In Álbora and as Geologists, we know the materials firsthand. As certified Project Management Professionals (PMP by PMI), we have regulated procedures that help us in the management of the project, and thanks to our extensive professional experience we know both sectors, Stone and Construction in the international markets.
If you need help, solve your doubts or any other question, do not hesitate to contact us.
What did you think of the post? Please, leave your comments!
No Comments